2012 Wire coating machine
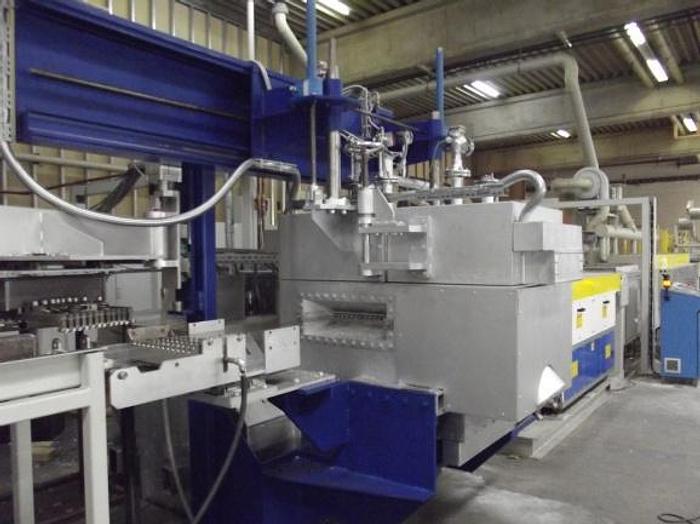
2012 Wire coating machine
Location:Cologne, Germany
Description
Wire coating (From a Plant for fire aluminizing steel wire)
The wire coating takes place in the coating device. The coating device is connected to the dosing oven via the riser pipe. The coating device consists of the pre-chamber, the coating tank, the nitrogen stripping device and the cooling device. The coating tank is closed by a movable cover. The pre-chamber, the coating tank and the covers are heated electrically. The temperature in the processes is adapted to the melting temperature of the dosing furnace. The temperature is measured via 2 redundant NiCrNi thermocouples in the pre-chamber, 2 redundant thermocouples in the heating of the coating tank, 2 redundant thermocouples in the heating bonnet of the coating chamber. The thermocouples query the respective process temperature. The heaters are controlled via setpoint - actual value comparison.
The pre-chamber is the connection between the coating part and the inductive preheating. The pre-chamber is sealed gas-tight, forming gas (95.5 % nitrogen, 4.5 % hydrogen gas) is fed into the pre-chamber) The forming gas has a weak reducing effect on the red-hot wire and acts as a protective gas to prevent oxidation of the red-hot wire The gas is discharged at the inlet openings of the inductor. The gas overpressure in the pre-chamber is preset manually using a control valve and can be read visually on a pressure gauge. In the pre-chamber there are guide nozzles axially aligned with the actual nozzles of the coating device
The coating nozzles of the coating device are mounted 12 times on a nozzle carrier and are used as a unit. The internal diameter of the nozzles is adapted to the wire diameter. The nozzles prevent molten aluminium from escaping from the actual coating tank; on the outlet side, the nozzles wipe off the excess aluminium. After filling the coating tank with molten aluminium (see A04), a side channel compressor creates a vacuum above the molten aluminium in the coating tank. The vacuum prevents excess aluminium from escaping from the nozzles, thus influencing the thickness of the aluminium layer on the wire. In the event of a possible wire breakage, the vacuum prevents the molten material from escaping from the free nozzles.
The vacuum is adjusted to the metallostatic pressure in the coating tank and the required layer thickness on the wire. The filling of the coating tank is monitored and controlled by 2 redundant distance sensors. The temperature control and monitoring of the heating is carried out via renundant thermocouples.
The front cover of the coating device can also be opened during coating operation for the purpose of inspection, slag removal and monitoring. The coating device always remains closed during coating operation. The operating states of the coating device are monitored and controlled by sensors for temperature, fill level and vacuum. Control is centralised via the DCS (process control system). The replenishment of used molten material through the wire coating is carried out automatically by the filling level monitoring in the coating chamber and pressure increase in the dosing furnace through the riser pipe. When the system is stopped or the nozzles need to be changed, the excess pressure in the dosing furnace is released and the coating chamber empties into the dosing furnace through the riser pipe.
There is an inspection opening with a sealing cone in the coating tank. When the system is stopped, the inspection opening can be opened and contaminated residual melt can be drained from the coating tank. In heating and coating mode, nitrogen gas is introduced into the coating device at an overpressure of 5 mbar as oxidation protection to prevent oxidation of the graphite material in the coating tank. The coated wire is cooled atmospherically after exiting the coating chamber. If necessary, the coating thickness can be reduced and levelled using nitrogen stripping nozzles. With the stripping nozzles it is possible to control the coating thickness of each wire independently.
If necessary, the device can be swivelled completely out of the line.
Find more here - https://www.ucymachines.com/
Specifications
Manufacturer | Wire coating machine |
Year | 2012 |
Condition | Used |
Stock Number | 78 |