KALTENBACH KF 2506 Plate Drilling Machine
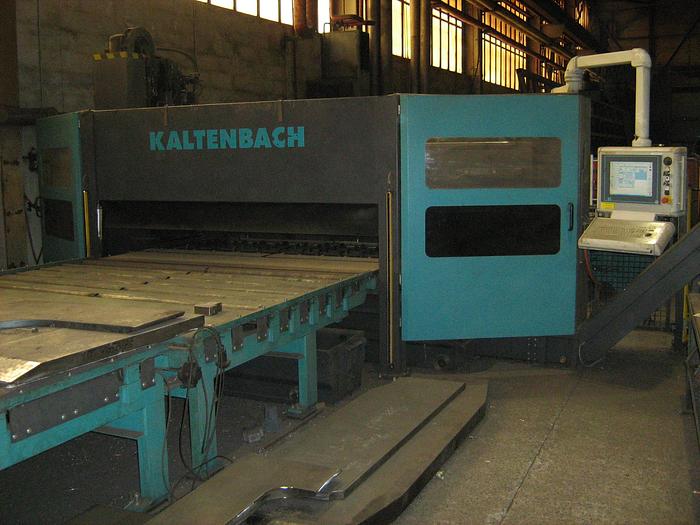
KALTENBACH KF 2506 Plate Drilling Machine
Contact us for price
Dresden, Germany
Description
KALTENBACH KF 2506
SHEET METAL PROCESSING CENTRE
Plate drilling system
The KF sheet metal processing centre was designed for the special market requirements of steel, machine and apparatus construction and is suitable for the efficient drilling and flame cutting of sheet metal, sheet metal strips and flat steels for end plates, base plates and gusset plates.
a) Technical data
sheet metal starting material: 220 - 2.500
Sheet width mm Length mm 500 - 6.000
Thickness mm 6 - 60
Stucco weight max kg 7.000
Prefabricated sheet metal parts:
Width x length min mm 130 X 130
max mm 2.500 X 2.000
Vertical (Y-axis) Słuck 1
Drilling diameter mm 8 - 50
Spindle speeds, frequency-controlled...... min-1/Rapid feed/rapid retraction mm/min 150 - 2000
Drill spindle feed mm/min O - 2000
Drill spindle positioning rapid traverse mm/min 24.000
Magazine place Słuck 6
Clamping force N 14000
Positioning speed max. mm/min 15000
Rapid traverse max mm/min 30000
customer-side bar 8
in standardised condition according to DlN1343 approx. I/min 350
Drill drive, frequency-controlled kW 26,0
Hydraulic unit (output 25 I/min) kW 24,0
Feed roller conveyor
or sheet lengths up to max mm 6000
Discharge roller conveyor
tor sheet lengths up to max mm 2000
Working height
Upper floor mm 800
Weight
Machine without accessories approx. kg 12000
System dimensions
Lx W x H (without cross transport panel) ...... approx. mm 15,000x8,000x2,900
Electrical equipment
to EN 60204-1 with free-standing switch cabinet and swivelling control panel
Electrical connection: 3 phases, neutral conductor, earth V/Hz 400/50
b) Basic machine equipment
- Machine portal designed as a stable welded construction to accommodate a vertical drilling unit.
- Drilling unit, in a positioning slide, running in backlash-free pretensioned linear roller guides.
- Fast and highly precise drill spindle positioning via ball screw and servomotor.
- Programmed spindle speeds, which are stored as fixed values in the operator software, are automatically assigned to the respective drilling diameter.
- Electro-mechanical drill feed Above ball screw and servo motor.
- Programmed drilling feeds, which are saved as fixed values in the operating software, are automatically assigned to the respective drilling diameter. It is also possible to manually increase or reduce the feed value specified by the programme on the control panel.
- Automatic drill length measurement by laser.
- Automatic tool change for 6 drill bit sizes. The tool changing unit consists of a disc magazine, which is attached directly to the drill carriage to achieve the shortest possible changing times.
The speed and feed rate change is automatically linked to the drill bit change. The scope of delivery includes 6 tool holders.
- Air cooling device with micro-metering system switched with the feed for drilling tools with internal axial air supply. Cooling is optionally available for drilling tools without axial air supply.
- Countersinking programme for the drilling spindle
Above drilling depth control for flat countersinks with interchangeable guide pins0 15 - 40 mm and
for countersinks with0 30 - 50 mm (countersink device required. Tools and holders are not included in the scope of delivery).
- Self-adjusting vertical clamping device with hydraulic hold-down device within the automatic cycle control.
- Chip scraper for automatic removal of the drilling chips from the workpiece surface, within the automatic cycle control. Automatic height adjustment on material surface.
- Chip holder can be pulled out on both sides of the machine on rollers, arranged in the machine bed.
- Torch cutting unit for oxy-fuel cutting, attached to the drilling unit, with remote torch ignition and flame monitoring, including the necessary cutting nozzles.
Fuel gas: e.g. propane, acetylene.
- Burner height adjustment. Automatic distance control with capacitive sensors.
- Feed of the flame cutting device via the positioning drive of the drilling unit.
- Slag trolley for centralised disposal of solids and burn-off, can be pulled out, mounted on rollers, arranged in the machine bed.
- Length measuring device, consisting of a gripper carriage with hydraulic double collet on the fixed system side and a hydraulic single collet approx. 1200 mm away from the fixed system side. Gripper carriage positioning drive Upper servo motor with absolute encoder and precision measuring rack. Additional hydraulic collet on the fixed system side, travelling with the main collet carriage.
- Sheet length measurement with laser light sensor by return travel of the additional collet on the fixed system side. Position detection of the lateral sheet edge on the fixed system side in the area between the drilling support and the flame cutting slot.
- Feeding roller conveyor in a solid, welded construction with maintenance-free, ball-bearing mounted transport rollers. Vertical stop cams for aligning the sheets on the fixed feed side. After the sheet has been clamped by the grippers of the length measuring system, the vertical stop cams are lowered automatically to avoid a copying effect of the contour of the sheet edge on the fixed support side during the machining process.
- Discharge roller conveyor in a solid, floating construction with maintenance-free, ball-bearing mounted transport rollers, fitted with intermediate plates
- Tipping device in the area of the outfeed roller conveyor, for automatic disposal of small parts (approx. 60 x 60 mm min. to 400 x 400 mm max., max. sheet thickness 60 mm) into a pull-out good parts container.
- Cooling unit for main switch cabinet and switch cabinet on the machine (required if ambient temperature exceeds + 35° C)
.
- Safety devices such as light grids and fences are included in the scope of delivery in accordance with CE regulations.
Machine control for KF sheet metal processing centre
hardware
- CNC path control for positioning the 2 axes in the sheet metal plane:
Y tor the transverse movement of the drilling spindle, optionally tor the marking device
X tor the longitudinal movement of the workpiece
- Machine control (PLC)
for controlling the machine functions
- Machine industrial PC with WINDOWS XP embedded with keyboard, mouse,
screen integrated in the control panel, network card
- Remote diagnostics optionally possible (in order of Kaltenbach's preferred options):
◦ TearnViewer via the Internet (further information at www.teamviewer.com)
◦ Via a VPN connection to be provided by the customer (Microsoft VPN preferred)
◦ Via a telephone line to be provided by the customer (digital, analogue)
Software
The industrial machine PC contains the steel construction-specific LANTEK software package for creating programmes for the machine control. The program, which runs under Windows XP Professional ML, processes the entered workpiece data and uses it to generate the NC program for the sheet metal processing centre.
The programme package consists of the following modules:
- Lantek Expert li Cut Plus.
Interfaces:
- Interactive automatic or manual contour nesting.
- Macro language incl. 67 standard macros. Own macros can be created additionally.
- Collision control
- Economy and grid cutting for waste optimisation
- Automatic remnant panel generation
- Integrated component management and databases for material, panel and remnant panel stock.
- Optional piercing function or pre-drilling.
- Calculation of component area and weight, cutting times and costs
- List and label printouts
- Automatic management of the number of nested and non-nested components.
2D CAD module for creating nesting plans, incl. automatic contour checking and correction as well as automatic dimensioning
- DSTV NC data import
- DXF input/output module
- DWG - AutoCAD import interface
Find more here - https://www.ucymachines.com/
Contact us at - sales@ucymachines.com
Specifications
Manufacturer | KALTENBACH |
Model | KF 2506 |
Year | 2011 |
Condition | Used |