2023 Holzher DYNESTIC 7535
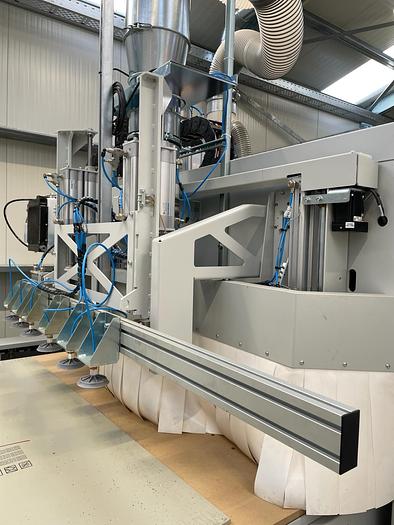
2023 Holzher DYNESTIC 7535
Contact us for price
Location:Nuremberg, Germany
Description
2023 HOLZ-HER DYNESTIC 7535 machining centre
The machine is one year old and has few operating hours
Machine frame in welded construction with ground and hardened prismatic guides for the travelling column, unit head and consoles
travelling column in gantry design
Rack and pinion drive, helical toothing, in X and Y direction,
1 x ball screw in the Z direction for precise positioning positioning
MATRIX table
Fixed, continuous machining table with grid division,
continuous grooves in the X and Y directions, groove spacing 50
mm with 25 metre sealing cord for clamping the wear plate
1 processing area with stop bars / stop
Height 30 mm, can be lowered pneumatically. 2 stop bars in the Y direction
and 1 stop in X-direction on the right (viewed from the front edge of the machine)
Remote maintenance:
Integrated network card for data transfer of control and programme data.
programme data. Data transfer takes place via high-speed Internet connection.
Prerequisite: High-speed Internet connection on the machine.
Use within the warranty period for warranty cases is free of charge.
USB connection for data backup or for direct import of machining programmes
processing programmes on the control panel.
TECHNICAL DATA
Processing dimensions 7535 10.5:
Max. Support surface on nesting table:
X = 3100 mm Y = 1560 mm
Max. Traverse paths:
X = 4695 mm Y = 2305 mm Z = 565 mm
Max. Processing height 7535/7735 Classic without pusher
(pusher)
Z = 300 mm from top edge of table (without wear plate)
Max. Max. overtravel height of the pusher over the table of the
Push/Auto/Lift versions:
Z = 250 mm from the top edge of the table (without wear plate)
Maximum programmable speed
Vector speed: 128.0 m/min
X = 80 m/min, Y = 100 m/min, Z = 25 m/min
SOFTWARE
CAMPUS V7 Plus CAD/CAM software 1 x licence incl. material removal simulation
1 software licence secured via licence plug for the machine
CAMPUS V7 PLUS, software for CNC machining centres
Consisting of:
1. CAMPUS NC-HOPS
2. CAMPUS aCADemy
3. cAMPUS MT-Manager
4. cAMPUS Workcenter
V7 PLUS =
5. cAMPUS 3D material removal simulation BetterSim
CAMPUS NC-HOPS
Graphical variant system with WOP and CAD/CAM properties for the creation of part variants with
macro technology KP
Hi-Speed USB-Device Network-Server
Allows the CAMPUS Single licence to be used on the machine
machine or an office computer in the same network.
One licence can be used in the network at a time!
CAMPUS V7 Plus CAD/CAM software 1 x licence incl.
BetterSim material removal simulation
1 x software licence secured via dongle for office or machine
machine
CAMPUS V7 PLUS, software for CNC machining centres
Consisting of:
1. CAMPUS NC-HOPS
2. CAMPUS aCADemy
3. cAMPUS MT-Manager
4. cAMPUS Workcenter
V7 PLUS =
5. cAMPUS 3D material removal simulation BetterSim
CAMPUS NC-HOPS
Graphical variant system with WOP and CAD/CAM
Features for creating part variants with macro technology
3.100,00 €
CAMPUS NESTING SOFTWARE
KP
CAMPUS V7 "BetterNest" free-form nesting software
1 pc. software licence secured via USB dongle for office or machine
machine
Free-form nesting software with:
Nesting of free-form parts possible
Import and generation of finished programmes
Mould approach and departure technology
Report and labelling
Configurable reports for overall nesting results
BOHRAGGREGAT
*
Pressure booster
Increase of the standard pressure from 6 to 8 bar
*
Drilling unit 7882, 16 spindles
Drive power 6 kW / 100 Hz
10 vertical spindles can be called up individually
L-shaped arrangement, 6 in X and 4 in Y direction, 32 mm grid
Max. Drill diameter: 35 mm
6 horizontal spindles
2 double drilling spindles in X-direction
1 double drill spindle in Y-direction
Total length of the drill: 70 mm from the screw-on end
(depending on the panel thickness)
Spindle stroke: 70 mm
Direction of rotation: Alternating clockwise / anti-clockwise rotation
Holder: M 10 thread - 11 mm fit
Without tools, without holder
*
Saw unit
Integrated sawing unit for sawing / grooving in X-direction
n(max.) 1000 - 5650 min-1 infinitely variable
Tool holder: A = max. Ø = 125 mm, I Ø = 20 mm,
B = max. 4.0 mm
Display of the operating status
by means of colour-changing LED lights in the machine hood
*
Electronic stop monitoring for all selected stop
stop bars or stop pins selected on the machine.
Safety device to prevent damage to the stops.
damage to the stops.
*
Hand-held control unit for remote control of the machine (13 m)
with the following operating functions:
> Start / stop of the machining programme
> Speed control of the processing cycles
> Reset button
> Manual feed / rapid traverse for all axes
> EMERGENCY STOP
*
Control panel with 21.5" 16:9 touchscreen
-Capacitive multi-touch screen for intuitive operation
-Continuous glass surface
-Incl. wireless QWERTY keyboard and mouse
(for CNCs with safety mats, the control panel is mobile
equipped #506 23 61)
5-axis head 7844, power: 13 kW (S6)
n(max.) = 0 - 24000 min-1 infinitely variable
cardanic; C-axis +/- 360° rotatable, A-axis +/- 180° rotatable
Liquid cooling (cooling unit included) with HSK-F 63 tool holder with right-hand threaded nut
threaded nut
(for clockwise rotating tools) with collet chuck with HSK shank, ceramic ball bearing (hybrid bearing)
Tool weight max. 6 kg (incl. holder),
Milling tools: max. Ø 200 mm
Saw blades: max. Ø 350 mm with optional 7886 pick-up changer
ChipControl - Bluetooth spindle sensor to prevent spindle damage
spindle damage due to vibrations or overheating.
Signals vibrations of the spindles via an alarm on the operator terminal
spindles, e.g. caused by unbalanced tools or broken cutting edges.
occur. The sensor chip also generates a warning signal if the spindle
spindle or bearing overheating.
Perfect in combination with the viaCockpit digitalisation package
and the option of displaying these messages for prevention purposes on the viaCondition module on mobile devices.
Tool changer 7875, 14-position linear pick-up
pneumatically liftable; max. tool weight: 5 kg / tool or
60 kg when fully loaded
Can be fitted with collet chuck with HSK shank
DYNESTIC 7535 series
Enormous flexibility and maximum user-friendliness. Precision and
years of operational reliability thanks to high-quality components such as covered,
hardened and ground linear guides on all axes. Optimised, extremely rigid machine and travelling column uprights for excellent machining results. Precision ball screws for the Z-axis,
helical ground rack in X and Y direction = high-precision machining over the entire machine length.
machining over the entire machine length. Only with HOLZ-HER CNC: 10 year guarantee on all linear guides!
Control technology and operation
State-of-the-art control and drive technology with powerful direct drives on all axes.
on all axes. Extremely high acceleration values and dynamics - all axes fully interpolating.
Automation and material handling
Extensive automation components optimise the work processes of the Dynestic
Dynestic series for high material throughput. Feeding can be carried out
via a lifting table as well as via intelligent area storage with vacuum
with vacuum lifters. Of course, HOLZ-HER also offers
software solutions for full integration into the operating process.
Milling and drilling units
High-torque routing units with excellent performance curves and extremely smooth running
smooth running transform their creativity into products with the highest
processing quality. The drilling unit is designed for short cycle times and for short cycle times and varied machining operations.
Machine table and tool changer
Precisely milled "high-flow vacuum table" for efficient and secure holding of workpieces.
of the workpieces. The stop pins are anodised and guided in hardened and adjustable eccentric
adjustable eccentric bushes for permanently accurate zero points. Fixed
changers and optional travelling tool changers ensure short tool change times.
short tool changing times. Pneumatically controlled cover of the HSK tool holders
as protection against contamination.
Units and tool technology
High-quality changing units from the accessories price list complement the CNC machine
and offer the user even more flexibility and reduced machining times.
Accessories and maintenance
HOLZ-HER machining centres can be configured from the respective modular system for
HOLZ-HER machining centres can be configured for a wide range of material and customer requirements. The extensive range of accessories also includes, for example, a variety of helpful and and tried-and-tested clamping devices for all areas of application.
Find more here - https://www.ucymachines.com/
Contact us at - sales@ucymachines.com
Specifications
Manufacturer | Holzher |
Model | DYNESTIC 7535 |
Year | 2023 |
Condition | Used |
Stock Number | 1146 |